В четверг, 16 ноября, в Самарском университете имени Королева (вузе - участнике национального проекта "Наука и университеты") состоялось открытие Технологического центра аддитивного производства, который войдет в создаваемую в России Национальную сеть технологических центров аддитивных и сопутствующих технологий. Это второй подобный центр в нашей стране. Первый был открыт в ноябре 2022 года на базе Технологического университета имени Леонова в городе Королеве Московской области.
Одной из задач центра станет создание высокотехнологичного производства деталей и узлов газотурбинных двигателей. Разработанная для данного центра система позволит сократить сроки подготовки производства деталей более чем в два раза, при этом трудоемкость и производственные издержки снизятся на 30-40%.
По словам директора Института двигателей и энергетических установок Самарского университета имени Королева Виталия Смелова, открывшийся сегодня центр оснащен передовым отечественным оборудованием в сфере аддитивных технологий, позволяющим оперативно решать задачи импортозамещения и воплощать из отечественных металлопорошковых смесей самые смелые конструкторские решения по заказу промышленных предприятий.
- Потенциальные сферы использования оборудования центра - двигателестроение, производство деталей и комплектующих для авиационной и космической техники, атомной энергетики, нефтеперерабатывающей и нефтегазодобывающей промышленности, - добавил он.
Виталий Смелов говорит, что компетенции сотрудников центра и имеющееся оборудование смогут обеспечить полный производственный цикл изготовления деталей и комплектующих. Аддитивные технологии позволяют в минимальные сроки выпускать изделия самой сложной формы, в том числе деталей с внутренними каналами или топологически оптимизированные конструкции.
Основное оборудование центра на данный момент - установка прямого лазерного выращивания ИЛИСТ-L, разработанная и изготовленная в Институте лазерных и сварочных технологий Санкт-Петербургского государственного морского технического университета. Установка представляет собой высокопроизводительный промышленный комплекс, рассчитанный на работу с жаропрочными сплавами, нержавеющими и высокопрочными сталями.
С помощью такого роботизированного комплекса можно изготавливать крупногабаритные детали диаметром до 1300 мм, высотой до 600 мм и весом до 1500 кг. При этом производительность выращивания весьма высокая - до 2,5 кг/ч. Луч высокомощного лазера расплавляет металлический порошок, в результате быстрого нагрева и охлаждения внутри материала формируется мелкозернистая структура, обеспечивающая высокую прочность выращенных изделий.
На установке можно создавать сложнопрофильные тонкостенные изделия, а также так называемые градиентные изделия - с переменным запрограммированным химическим составом и физическими свойствами. Механические свойства получаемых деталей будут на уровне штампованных, без пор и трещин, а в процессе выращивания можно наносить на поверхности изделия необходимые функциональные покрытия. Кроме того, можно создавать гибридные конструкции, комбинируя аддитивные и традиционные технологии - сварку, литье, штамповку, механическую обработку. Снижение числа технологических операций при изготовлении деталей и конструкций сложной формы существенно увеличит производительность при меньших материальных, энерго- и трудозатратах.
- Переход к новым интеллектуальным технологиям позволяет организовать высокопроизводительное производство на базе совокупности технологий, когда в зависимости от требований к функциональным свойствам деталей будут использоваться как аддитивные, так и комбинированные аддитивные технологии, - отметил директор Института двигателей и энергетических установок. - Конструкция ключевых деталей современной аэрокосмической техники будет учитывать технологические возможности аддитивных технологий в области получения заготовок деталей со сложной геометрией наружных и внутренних поверхностей, что позволит применить элементы топологической оптимизации и концепции "умного" дизайна при их проектировании, повысить их технологичность и сократить количество деталей и сборочных единиц.
Одним из проектов, которые будут реализованы в самарском центре, станет создание совместного с предприятием "ОДК-Кузнецов" высокотехнологичного производства деталей и узлов горячей части индустриальных газотурбинных двигателей с повышенными функциональными характеристиками. Проект реализуется по соглашению с Минобрнауки России. В рамках проекта ученые Самарского университета имени Королева уже разработали интеллектуальную систему сопровождения конструкторско-технологической подготовки производства.
- В этой системе задействованы многопараметрические цифровые двойники двигателей и их компонентов, что упрощает оптимизацию конструкции и внедрение на предприятии новых или усовершенствованных процессов изготовления ключевых деталей газотурбинных двигателей. По предварительным данным, система позволяет сократить сроки подготовки производства более чем в два раза, при этом трудоемкость и производственные издержки снижаются на 30-40%, - подчеркнул Виталий Смелов.
В настоящее время специалисты центра отрабатывают комплексные технологии аддитивного производства деталей и узлов горячей части перспективных газотурбинных двигателей на базе технологий селективного лазерного сплавления и прямого лазерного выращивания. Часть деталей в университете по новым технологиям уже изготовлены и прошли предварительные испытания в составе узла малоэмиссионной камеры сгорания, например внутренний кожух камеры сгорания газотурбинного двигателя НК-36СТ разработки "ОДК-Кузнецов", широко используемого в нашей стране в составе газоперекачивающих агрегатов. Кроме этого, в центре изготавливаются заготовки деталей малоразмерной газотурбинной установки - турбогенератора малой мощности для нужд распределенной энергетики, малоразмерного газотурбинного двигателя тягой 20 кгс.
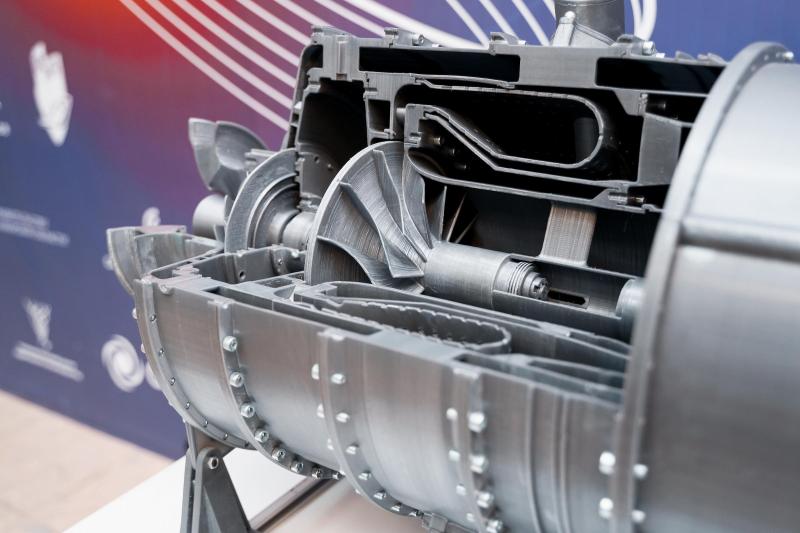
Фото: предоставлено пресс-службой Самарского университета имени Королева